PRINTING THE FUTURE
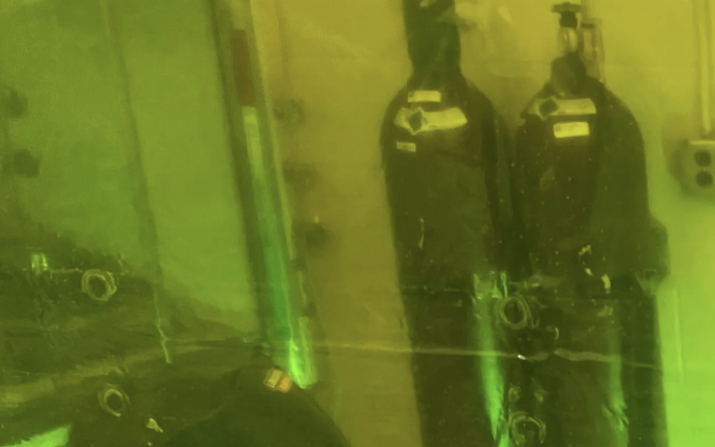
PRINTING THE FUTURE
Case students hope to fortify metal 3D printing with a low-cost, open-source machine Sparks flew from a gangly apparatus that laid down a thin layer of steel, one after the other, as it noisily built what might become a boat propeller or a rocket body in the basement of the White building.
3D printing with metals has been evolving rapidly, but a multidisciplinary team of students at the Case School of Engineering is stoking the craft. They have designed and built a machine they believe can print metal more affordably and efficiently, which in turn could make the technology more widely available.
Vishnu Ramasamy, a doctoral student in the Department of Materials Science and Engineering, leads the team behind Arc One. It is Case’s contribution to Wire Arc Additive Manufacturing, or WAAM, which is a wire-based metal 3D printing process.
Not only is the Arc One cheaper than industrial metal printers, Ramasamy said, the design and operating software are open source. That means anyone can build their own version and use Arc One’s software to start experimenting with processes and materials.
“This is a highly research-focused machine,” he said. “In addition, this could be an excellent teaching platform. We even expect research teams to use this machine to prove concepts before they decide to buy an industrial WAAM printer costing over a half million dollars.”
Lincoln Electric is one of the companies supporting the project by providing welding equipment. Rockwell Automation is also interested in what’s sparking behind the welding curtain in the Advanced Manufacturing and Mechanical Reliability Center (AMMRC) in the Charles White Metallurgy Building.
“We’re happy to try to help with this,” said Marzel Brown ’96, Rockwell’s global academic enablement manager, who attended a recent demonstration.
Brown said the innovations could help make metal printing more commonplace in factories, where Rockwell’s technology could add precision to the production process.
Once completed, the machine will support the National Science Foundation’s ERC program – HAMMER at Case, led by Professor John Lewandowski, which aims to add new efficiencies to the nation’s factories.
Meanwhile, the Arc One team is trying to raise $3,000 to pay for equipment, student workers and to help validate the idea for larger funders. The students have started a crowdfunding campaign on GiveCampus, where they are asking for modest donations. Once they reach the $3,000 goal, they will receive funding from NASA to complete the project. That campaign can be found HERE.
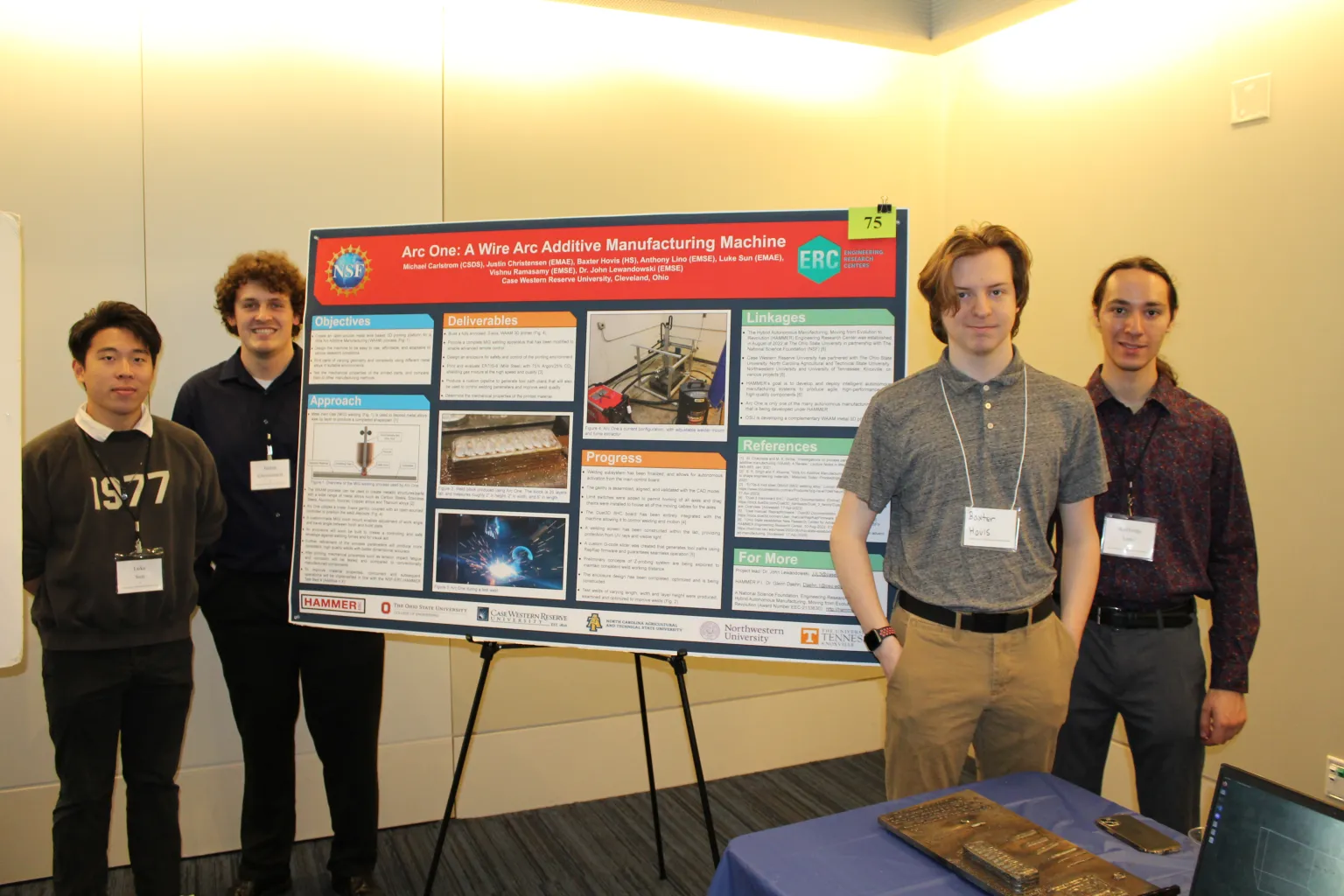
The Arc team exhibited its technology at the Summer 2023 Intersections Poster Session August 3.
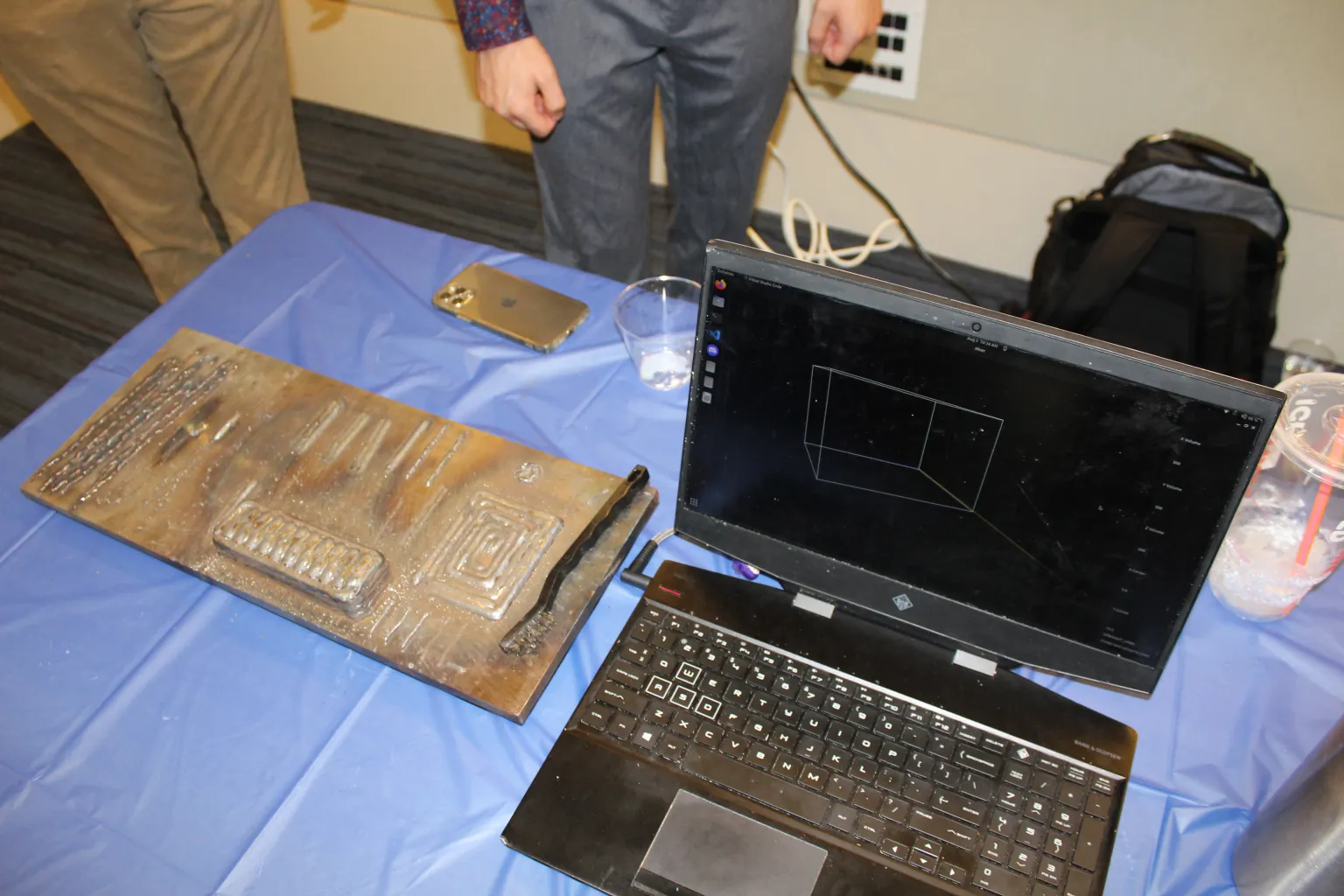
A sample, left, of metal lines drawn by the Arc One.