- Fatigue and Fracture of Implantable Cables
- Effects of Thermal Exposure on Sensitization and Environmentally Assisted Cracking (EAC) in Al-Mg (5XXX series) Alloy
- Mechanical Behavior of 5XXX Alloys Removed from the HMCS Iroquois
- Microstructure Informatics of Additively Manufactured (AM) Metal Alloys
- Nitinol Commercialization Accelerator
- Development of an Ecosystem for Qualification of Additive Manufacturing Processes and Materials in Aviation
- In-Situ Alloying of GRCop-42 via Additive Manufacturing
- Process-Structure-Property Study on CP-Ti Produced via High Deposition AM Laser Hot-Wire (LHW)
- Process-Structure-Corrosion/SCC Property Study of High Deposition Rate AM 316L
- Accelerating Maturation of Advanced Manufacturing for Low Cost Sustainability (MAMLS) Direct Part Production: Effects of Defects in Laser Powder Bed Fusion of AlSi10Mg
- ULTIMATE Refractory Alloys: Innovation, Science, and Engineering (RAISE)
- NSF-IURCR on Materials Data Science (MDS)-RELY on Stress Corrosion Cracking of Al-Mg Alloys Under Two Enviornmental Conditions: Studied at Diamond Light Source (UK) Using XCT
Recent:
- Hydrostatic Extrusion of Nano-ODS Steel
- ICME Enhanced Development of TiAl for Advanced Aerospace Components
- Processing for Assured Properties of 3rdGeneration Al-Li Alloys
- Development of Cost-effective, Advanced Mechanical Alloying, Powder Consolidation Processes for Sub-micron Powder Reinforced Al MMCs
- Rapid Qualification Methods for Powder Bed Direct Metal AM Processes
- Alloy Design for High Density Metallic Glasses/Composites with High Toughness
- Size Scale and Confinement Effects on Plasticity and Fracture in Metallic Glasses
- Fracture and Fatigue of Lightweight Alloys for Energy Storage
- Ultrasonic Bonding of Amorphous Metal Foils
- US-Egypt Collaborative Grant - Processing and Mechanical Properties of Amorphous Metal Foil and Laminates
- Damage Tolerant Structural Amorphous Metals: Intrinsic and Extrinsic Approaches for Ultralight Systems
- Low Mass Aerospace Ball Bearing Retainer Development
- Ultra-high Temperature Refractory Alloys for Aerospace Applications
- High Performance Corrosion Resistant Coatings
- Effects of Changes in Strain Rate and Test Temperature on Mechanical Behavior of HSLA-65 Steel Relevant to Friction Stir Welding Condition
- Ultra-high Temperature Metallic Glasses
- Fundamantal Approaches to Design of Tough Fe-based Metallic Glasses
- Effects of Interfaces on Blast Resistance of Amorphous Metals
- Fracture and Fatigue of Amorphous Aluminum Alloys
1. Fatigue and Fracture of Implantable cables
A team of materials scientists is supporting the development of Networked Implantable Neuroprostheses (NNPS) Systems on an NIH-Bioengineering Research Partnership with the Cleveland Functional Electrical Stimulation (FES) center. The Materials Group is leading the material and structural evaluation, analysis, and testing of implantable leadwires and interconnects that form part of the NNPS. Currently the potential use of silver cored Drawn Filled Tube (DFT) cables as leadwires is being investigated. The response of various configurations of the DFT cables to static and cyclic mechanical loading imposed during long-term implantation is being studied experimentally. Evaluation of mechanical integrity of interconnects that joins the leadwires with the various modules of the NNPS system is also currently underway.
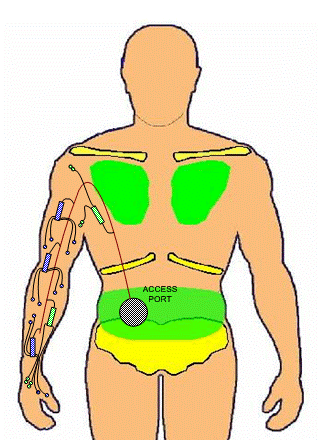
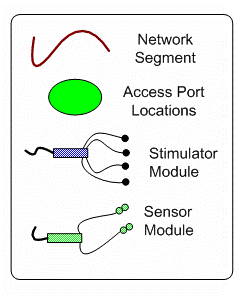
Upper Extremity NNPS
Electrodes for NNPS
(Images coutesy: Cleveland FES center )
Tension and fatigue behavior of DFT cables with various configurations as shown below are under investigation
(Images coutesy: Fort Wayne Metals)
7x7 implantable cable tested in Flex tester
(Image coutesy: http://www.fortwaynemetals.com)
For more information:
Conference Posters:
- Neural Interfaces Conference 2008 poster
- Research ShowCASE 2008 poster
- IFESS 2007 poster
- Research ShowCASE 2007 poster
- Research ShowCASE 2006 poster
Journal Papers
- Fracture and Fatigue of Implantable 316LVM 1x7 cable
- Fracture and Fatigue of Implantable Composite DFT cables
2. Effects of Thermal Exposure on Sensitization and Environmentally Assisted Cracking (EAC) in Al-Mg (5XXX series) Alloys
Support: ONR
The effects of thermal exposure (T, time) on sensitization and resulting mechanical behavior of commercial Al-Mg (5XXX series) alloys is being determined under quasi-static and cyclic conditions in various environments (e.g. dry air, humid air, solutions). Microstructural changes are being documented using SEM-EBSD as well as TEM on both as-received and thermally exposed materials. EAC behavior is being evaluated using ASTM standardized test techniques while various remediation strategies (e.g. thermal reversion, laser treatment, etc.) are being explored to reverse the effects of sensitization in attempts to recover the properties.
Conference Posters:
- Sensitization Effects on the Microstructure and Mechanical Properties of 5xxx Aluminium Alloys
- Microstructure and Mechanical Properties Evolution of Long-Time Serviced 5xxx Aluminium Alloys
Journal Papers:
3. Mechanical Behavior of 5XXX Alloys Removed from the HMCS Iroquois
Support: ONR
The HMCS Iroquois was decommissioned after 42 years service. Various parts of the superstructure were constructed from Al-Mg (5XXX series) alloys. Plates have been received from various sections of the superstructure (e.g. exposed to sunlight/weather, shielded from sunlight/weather, etc.) and the microstructure and mechanical properties are being evaluated on samples excised from those plates. Microstructural details are being documented using SEM-EBSD as well as TEM while environmentally assisted cracking behavior is being evaluated using ASTM standardized test techniques.
4. Microstructure Informatics of Additively Manufactured (AM) Metal Alloys
Support: MRL, LLC-NAVAIR
The effects of changes in AM processing conditions on Powder Bed Fusion (PBF)-processed alloys is being determined in collaboration with MRL, LLC. The effects of changes in power (P) and velocity (V) on the defect characteristics (e.g. size, density, distribution) and resulting microstructure are being systematically evaluated on both as-deposited and post-processed (e.g. HIP) material.
5. Nitinol Commercialization Accelerator
Support: Ohio Third Frontier
The Ohio Third Frontier Wright Projects Program has funded a collaborative effort between the Cleveland Clinic, CWRU, University of Toledo, NASA Glenn Research Center, and Norman Noble, Inc. in order to develop a better understanding of the metallurgical processing and mechanical characterization of nitinol for use in biomedical and aerospace applications. Biomedical applications range from orthodontia to implantable devices while higher temperature shape memory alloys are of interest for aerospace. The collaboration is designed to create synergy amongst collaborators in the research and development of nitinol products. CWRU is developing a facility wherein the effects of composition changes on mechanical performance can be determined. The laboratory housed at CWRU’s Materials Science and Engineering Department contains processing and characterization (thermal and mechanical) equipment that allows for the manufacture and analysis of nitinol products
6. Development of an Ecosystem for Qualification of Additive Manufacturing Processes and Materials in Aviation
CWRU is examining the effects of various Laser Power (P)-Velocity (V) combinations on the fatigue and fracture behavior of Laser Powder Bed Fusion processed Ti-6Al-4V in a NASA- University Leadership Initiative (ULI) led by Carnegie Mellon University (https://techport.nasa.gov/view/96111). Fatigue S-N behavior is being analyzed with quantitative descriptions of process-induced defects and their effects on fatigue life. Novel testing techniques and fracture surface quantification are being used to quantify the effects of process-induced defects on fatigue life.
7. In-Situ Alloying of GR-Cop-42 via Additive Manufacturing
This NASA-NSSC funded project examines in-situ alloying of GRCop-42 via Additive Manufacturing approaches. Multiple researchers in the in-situ alloying space have identified an increased energy to additively manufacture (AM) metals from their elemental powders versus from a pre-alloyed powder. Authors suggest sources of the increased energy demands during in-situ alloying could be elemental versus alloy optical and thermal properties, need for aggressive convection, and net energy of in-situ reaction. Literature currently lacks an energy-based approach to understanding in-situ alloying. This work aims to fill this gap by augmenting Rosenthal-based models for melt pool size and temperature with two major pieces of in-situ alloying: elemental optical and thermal properties and net in-situ reaction energy. GRCop-42 provides a test case of in-situ alloying, with its single reaction to form Cr2Nb and a simple alloy chemistry. It is hypothesized that this augmented melt pool model will better agree with empirical melt pool trends and therefore provide some analytical justifications for the differences in energy demand of in-situ alloying via AM versus AM of pre-alloyed powders.
8. Process-Structure-Property Study on CP-Ti Produced via High Deposition AM Laser Hot-Wire (LHW)
Laser hot wire, a layer-by-layer material deposition process, is an efficient process for high volume deposition to generate both freestanding parts and to effect repairs (especially when low net heat input is required). Both are derived from the highly-controllable net heat input, which also permits unique metallurgical control. Wasted material is minimized (e.g. no over spray) and final structures include strong metallurgical bonds, corrosion- and wear-resistance. The process has been demonstrated at Lincoln Electric's headquarters in Cleveland, OH, depositing a titanium alloy to meet ASTM specifications for nitrogen and oxygen contents and mechanical properties. This ONR-funded project is examining the Process-Structure-Property relationships for CP-Ti Grade 2 Produced via High Deposition AM Laser-Hot Wire (LHW).
9. Process-Structure-Corrosion/SCC Property Study of High Deposition Rate AM 316L
316L produced via conventional wrought-processing techniques is a workhorse material that is used in a variety of DoD and commercial applications. The advent of additive manufacturing (AM) provides the opportunity to deposit materials for local repairs as well as build larger volumes depending on the type of AM process (e.g. PBF vs. DED). In particular, the availability of certain Directed Energy Deposition (DED) additive manufacturing wire-fed approaches (e.g. Sciaky, Laser Hot Wire (LHW), Wire and Arc AM (WAAM)) can provide build rates of 15-20 lbs./hour. This work is conducting a systematic study of WAAM-processed 316L in a variety of build conditions relevant to a number of naval applications where wrought material is typically used, requires repair, or is being considered for use. WAAM processing will be used to prepare bulk deposits in order to determine the effects of changes in WAAM parameters on the resulting microstructure (grain size, carbide precipitation/sensitization) and properties (hardness, tension, toughness, fatigue, corrosion/SCC resistance), with comparisons to the behavior of laser powder bed fusion-processed 316L being conducted in other ONR-sponsored work.
10. Accelerating Maturation of Advanced Manufacturing for Low Cost Sustainability (MAMLS) Direct Part Production: Effects of Defects in Laser Powder Bed Fusion of AlSi10Mg
The objective of this America Makes sponsored research program, led by Youngstown State University is to conduct collaborative work amongst team members to accelerate part production of additively manufactured AlSi10Mg samples/parts using the powder bed fusion (PBF) process. This research is investigating the source(s) of defects and their effects on subsequent mechanical performance. Samples have been prepared with different levels of defect density in order to examine the effects of such process-induced defects on the tension, S-N fatigue, fatigue crack growth, and fracture toughness.
11. ULTIMATE Refractory Alloys: Innovation, Science, and Engineering (RAISE)
Development of advanced technologies for improving power generation gas turbine (GT) efficiency is strategically important to energy security in the United States. In 2018, GT facilities powered by natural gas generated 34 % of the electrical power, and are projected to continue growing the share to 39 % in 2050 to meet the growing energy demand. Ultrahigh temperature metallic materials and coatings are among the critical enabling technologies for achieving 70 % combined cycle efficiency and more than 50 % simple cycle efficiency by allowing higher GT inlet temperatures. In order to enable the ARPA-E ULTIMATE goal of 1800 °C turbine inlet temperature, without sacrificing efficiency with an increased cooling flow, a team led by GE Global Research is working on a combination of breakthrough turbine blade material technologies, consisting of a 1300 °C capable Nb-base refractory alloy, a 1400 °C capable oxidation resistant BC, a 1700 °C capable TBC and a blade manufacturing process, based on in-depth scientific understanding and innovative engineering for industrial applications. CWRU is conducting research on fracture-critical properties with mechanical characterization studies that include room temperature strength and ductility, fracture toughness, and high temperature evaluations using hot microhardness testing.
12. NSF-IURCR on Materials Data Science (MDS)-RELY on Stress Corrosion Cracking of Al-Mg Alloys Under Two Environmental Conditions: Studied at Diamond Light Source (UK) Using XCT
The PI has obtained access to commercial Al-Mg alloy navy destroyer (HMCS Iroquois) ship plate that has been decommissioned after 42-years of service. In addition to various ASTM tests conducted at CWRU to establish the effects of such service on the stress corrosion cracking (SCC), corrosion susceptibility, and mechanical reliability of a particular plate location, in-situ tension experiments have been conducted at the Diamond Light Source (UK) to image the evolution of fracture under both dry (i.e. RH < 1%) and high RH (i.e. > 50%) SCC conditions. Time series images are available as a series of .tiff images exceeding 20 TB that document the starting material (e.g. inclusions, pores, etc.) as well as the evolution of fracture under both dry and SCC condition at high resolution. Data Science and ML techniques will be used to understand the evolution of fracture/SCC and its relation to various microstructural features in this commercial alloy used in a variety of DOE/DOD and other applications. In particular, the SCC susceptibility of this service-retrieved material addresses the reliability and lifetime assessment of materials after typical service history.
Recent:
1. Development of Cost-effective, Advanced Mechanical Alloying, Powder Consolidation Processes for Sub-micron Powder Reinforced Al MMCs
Support: LIFT/ALMMII-ONR
This project involves collaboration with Materion (project lead), Boeing, Lockheed-Martin, GKN, PSU, and MIT on various aspects related to the processing and subsequent properties of sub-micron powder reinforced aluminum MMCs. The CWRU project involves direct powder forging (DPF) experiments as a novel consolidation route in addition to evaluating the mechanical performance (e.g. tension, high cycle fatigue, etc.) of MMCs produced via various techniques (e.g. CIP, HIP, SPS, extruded, etc.). The DPF experiments are being conducted using unique equipment in the AMMRC to examine the effects of different forging conditions (e.g. T, strain rate, strain) on the consolidation of porous sub-scale billets of both Al-Mg-Si (i.e. 6XXX series) and Al-Cu-Mg-Si (i.e. 2XXX series) alloys reinforced with up to 40 volume percent SiC particulates. The mechanical behavior studies are focusing on the tension behavior of such MMCs consolidated by a variety of techniques, while the high cycle fatigue performance is focusing on an extruded Al-Cu-Mg-Si (i.e. 2XXX series) alloy with 25 volume percent reinforcement of SiC particulates.
2. Microstructure Informatics of Additively Manufactured (AM) Metal Alloys
Support: MRL, LLC-NAVAIR
The effects of changes in AM processing conditions on Powder Bed Fusion (PBF)-processed alloys is being determined in collaboration with MRL, LLC. The effects of changes in power (P) and velocity (V) on the defect characteristics (e.g. size, density, distribution) and resulting microstructure are being systematically evaluated on both as-deposited and post-processed (e.g. HIP) material.
3. Processing for Assured Properties of 3rd Generation Al-Li Alloys
Support: LIFT/ALMMII-ONR
This project involves collaboration with UTRC (project lead), University of Michigan, Ohio State University, and Arconic on various aspects related to processing of 3rd generation Al-Li alloys. The CWRU project involves mechanical evaluation (e.g. tension, compression, Charpy Impact) of sub-scale H-forgings in addition to the generation of a process map (i.e. T, strain rate, strain) for deformation processing of these alloys. Sub-scale cylindrical forging samples are being deformation processed using unique equipment in the AMMRC at CWRU in order to evaluate the effects of changes in processing conditions (i.e. T, strain rate, strain) on both the flow stress and resulting microstructures of the sub-scale forging samples. Various microscopy techniques, including EBSD, are being utilized to determine the effects of changes in processing conditions on the resulting microstructure and the likelihood of recovery and/or recrystallization during forging and/or subsequent heat treatment.
4. Development of Cost-effective, Advanced Mechanical Alloying, Powder Consolidation Processes for Sub-micron Powder Reinforced Al MMCs
Support: LIFT/ALMMII-ONR
This project involves collaboration with Materion (project lead), Boeing, Lockheed-Martin, GKN, PSU, and MIT on various aspects related to the processing and subsequent properties of sub-micron powder reinforced aluminum MMCs. The CWRU project involves direct powder forging (DPF) experiments as a novel consolidation route in addition to evaluating the mechanical performance (e.g. tension, high cycle fatigue, etc.) of MMCs produced via various techniques (e.g. CIP, HIP, SPS, extruded, etc.). The DPF experiments are being conducted using unique equipment in the AMMRC to examine the effects of different forging conditions (e.g. T, strain rate, strain) on the consolidation of porous sub-scale billets of both Al-Mg-Si (i.e. 6XXX series) and Al-Cu-Mg-Si (i.e. 2XXX series) alloys reinforced with up to 40 volume percent SiC particulates. The mechanical behavior studies are focusing on the tension behavior of such MMCs consolidated by a variety of techniques, while the high cycle fatigue performance is focusing on an extruded Al-Cu-Mg-Si (i.e. 2XXX series) alloy with 25 volume percent reinforcement of SiC particulates.
5. Rapid Qualification Methods for Powder Bed Direct Metal AM Processes
Support: National Additive Manufacturing Innovation Institute (NAMMI)
This collaborative project links 5 Universities, 5 Industrial members, and 2 Government Laboratories to target the missing links for understanding and controlling melt pool geometry, material microstructure and mechanical properties across both the Direct Metal Laser Sintering (DMLS) and Electron Beam Melting (EBM) additive manufacturing (AM) processes. Both DMLS (by EOS) and EBM (by Arcam) use a rapidly moving laser or electron beam to locally melt powder particles on top of a growing metallic part. Metal parts can be fabricated directly, with little or no user intervention. Establishing links between process variables, material microstructure and mechanical properties is essential to qualifying these processes for use in the aerospace and other industries. The primary achievement for this TRL 4-7 project will be to provide these links to current users of these processes in the U.S. aerospace industry (represented by Pratt & Whitney, GE Aviation and Lockheed Martin) and a broad group of companies considering whether and where to integrate direct metal AM into their production streams (represented by Kennametal and Bayer).This technical approach to understanding DMLS and EBM will be combined with first-edition AM cost analysis tools.
Our project goals are made possible by taking a unique modeling-based process mapping approach that will be integrated with resulting microstructure and properties in order to characterize and better understand these AM processes. That approach will be linked to not only on-site industrial part fabrication but also U.S.-leading research on AM process/property relationships at Carnegie Mellon University, Case Western Reserve University, Wright State University, North Carolina State University, the University of Louisville, Oak Ridge National Laboratory, and NIST. Six project tasks are identified to achieve these goals, while contributing to education and workforce development at partner institutions.
Recent Publication:
- Metal Additive Manufacturing: A Review of Mechanical Properties
- Overview of Materials Qualification Needs for Metal Additive Manufacturing
- Evaluation of Orientation Dependence of Fracture Toughness and Fatigue Crack Growth Behavior of as-deposited ARCAM EBM Ti-6Al-4V
- Process Mapping, Fracture and Fatigue Behavior of Ti-6Al-4V Produced by EBM Additive Manufacturing
- Microstructure and Mechanical Properties of Ti-48Al-2Cr-2Nb Manufactured Via Electron Beam Melting
6. Alloy Design for High Density Metallic Glasses/Composites with High Toughness
Support: DTRA
A team of investigators from University of Virginia, Carnegie-Mellon University, and CWRU are exploring predictive modeling techniques (CMU/UVa) to produce metallic glasses with both high density and high toughness. Alloys are being designed to produce materials with high poisson’s ratio, as this has been shown to produce metallic glasses with both high toughness (CWRU) and high plasticity (UVa). Alloys based on Ni-Ta, Co-Ta, and W-based glasses are being explored.
- Weibull modulus of hardness, bend strength, and tensile strength of Ni−Ta−Co−X metallic glass ribbons
- An improved method for calculation of elastic constants of metallic glasses
7. Size Scale and Confinement Effects on Plasticity and Fracture in Metallic Glasses
Support: ARO
The effects of changes in size scale and confinement on the plasticity and fracture behavior of metallic glasses is being determined. Confinement effects are being determined by testing metallic glasses in tension with different levels of superimposed hydrostatic stress. Recent work has extended this to conducting similar tests at high temperature in the presence of high hydrostatic pressure. Size scale effects are being determined on both micro- and nano-wires of metallic glass prepared in both our laboratory and collaborators. The effects of changes in size scale on the plasticity and fracture behavior are being determined.
Journal Papers:
- Sample size and preparation effects on the tensile ductility of Pd-based metallic glass nanowires
- Guiding and Deflecting Cracks in Bulk Metallic Glasses to Increase Damage Tolerance
- A Damage-tolerant Bulk Metallic Glass at Liquid-nitrogen Temperature
8. Fracture and Fatigue of Lightweight Alloys for Energy Storage
Support: Luxfer, USA
6xxx aluminum alloy cylinders for energy storage applications are being evaluated mechanically. Fracture and fatigue experiments are being conducted on samples excised from the cylinders over a range of strain rates and loading conditions on different compositions in order to determine the effects of composition and processing on the resulting properties.
9. Ultrasonic Bonding of Amorphous Metal Foils
Support: Boeing/DARPA
Ultra-lightweight amorphous metals are being bonded via a variety of ultrasonic techniques. The mechanical behavior of the amorphous metal foils are being determined both before and after bonding by using a variety of testing techniques including: Hot microhardness testing, tension testing, interface toughness measurements, interface strength measurements.
Conference Posters:
10. Damage Tolerant Structural Amorphous Metals: Intrinsic and Extrinsic Approaches for Ultra-Light Weight Systems
Support: DARPA
The effects of INTRINSIC and EXTRINSIC approaches to improving the balance of mechanical properties in ultra-light weight bulk metallic glasses is being investigated. INTRINSIC approaches include changing the elastic constants via chemistry changes in order to produce more ductile/tough systems. EXTRINSIC approaches include compositing in order to produce more energy absorbing systems.
Conference Posters:
- Intrinsic and Extrinsic toughening of BMGs
- Temperature and Loading Rate effects on the Mechanical Behavior of Ca based BMG
Journal Papers:
11. US-Egypt Collaborative Grant - Processing and Mechanical Properties of Amorphous Metal Foil and Laminates
Support: NSF International Collaborative Program
The effects of chemistry changes on the mechanical behavior of Fe-based metallic glasses are being determined in tension, bending, flex bending fatigue, and notched/precracked toughness. In addition, lamination studies are being conducted in order to improve the mechanical behavior of the Fe-based metallic glass materials.
Conference Posters:
- Effect of composition on mechanical properties of Fe based amorphous ribbon
- Fracture and Fatigue of Fe based metallic glass ribbon
12. Low Mass Aerospace Ball Bearing Retainer Development
Support: TIMKEN/AFRL
The fracture and fatigue behavior of candidate bearing retainer materials are being evaluated over temperature ranges relevant to potential applications.
Conference Posters:
13. Ultra-high Temperature Refractory Alloys for Aerospace Applications
Support: GE
The fracture and fatigue behavior of advanced Nb alloys are being determined over a range of test temperatures. Both SEM and Laser Confocal Microscopy are being used to characterize the microstructures and crack paths selected under monotonic and cyclic loading conditions.
Conference Posters:
14. High Performance Corrosion Resistant Coatings
Support: DoE
HVOF coatings have been prepared using Fe-based bulk metallic glasses. The performance of the coatings as well as drop cast ingots of the Fe-based bulk metallic glass have been determined over a range of temperatures using hot hardness and compression testing in addition to fracture toughness measurements. The effects of thermal exposures on microstructure evolution and resulting properties have also been determined.
15. Effects of Changes in Strain Rate and Test Temperature on Mechanical Behavior of HSLA-65 Steel Relevant to Friction Stir Welding Conditions
Support: ONR
The effects of changes in test temperature and strain rate on the flow stress of HSLA-65 relevant to friction stir welding conditions is being determined. Collaborative work with Prof. Vikas Prakash, Mechanical and Aerospace Engineering Department, is being conducted to devise experiments to probe the mechanical behavior of steels under conditions relevant to friction stir welding conditions.
Conference Posters:
High Strain/Temperature Experiments Relevant to Friction Stir Welding of HSLA-65
16. Ultra-High Temperature Metallic Glasses
Support: AFOSR
The effects of changes in composition on the glass transition temperature and mechanical behavior are being determined for a range of metallic glasses and test temperatures.
17. Fundamantal Approaches to Design of Tough Metallic Glasses
Support: University of Virginia/ONR
Description: The effects of systematic changes in the chemistry of Fe-based bulk metallic glasses on the toughness is being investigated. Systematic changes to the chemistry are being performed in order to change the elastic constants in a manner more conducive to plastic flow and enhanced toughness.
Journal Papers:
- Tough Fe based Bulk Metallic Glass
- Chemistry (Intrinsic) and Inclusion (Extrinsic) Effects on the Toughness and Weibull Modulus of Fe-Based Bulk Metallic Glasses
- Thermal Exposure and Test Temp effects on Structural evolution and Hardness/Viscosity of Fe based BMG
18. Effects of Interfaces on Blast Resistance of Amorphous Metals
Support: ONR
Description: The effects of interfaces on the energy absorbing characteristics of bulk metallic glasses are being determined. Both Zr-based and Fe-based bulk metallic glasses are being tested under quasi-static and high strain rate conditions via collaborations with Prof. Vikas Prakash in Mechanical and Aerospace Engineering at CWRU. Novel insert designs have been prepared for testing while ultra-high speed video (e.g. Up to 200,000,000 frames/sec) has been utilized to capture the deformation and fracture characteristics of these novel materials.
Conference Posters:
Journal Papers:
- Design of Inserts for Split-Hopkinson Pressure Bar Testing
- Effect of High Strain Rates on Peak Stress in Zr based BMG
- Effects of Annealing and Specimen Geometry on Dynamic Compression of Zr based BMG
- Spall Strength of Zr based BMG under Shock Induced Compression and Shear Loading
19. Fracture and Fatigue of Amorphous Aluminum Alloys
Support: Pratt & Whitney/DARPA
Deformation processing of amorphous aluminum alloy powders has been utilized to produce novel nanostructured aluminum composites. The effects of various processing conditions on the strength, toughness, and high cycle fatigue behavior is being determined at room temperature, 300F and 500F and compared to conventional aluminum alloys.
Conference Posters:
Journal Papers:
Effects of Changes in Chemistry on Flex Bending Fatigue Behavior of Al-Based Amorphous Alloy Ribbons